Guía de buenas prácticas de PRL en fabricación de cemento
En este tema, aprenderemos las buenas prácticas en prevención de riesgos laborales que se aplican en los distintos procesos de fabricación del cemento, a través de varios casos prácticos de las tareas más representativas en dicho proceso.
Índice
Metodología y desarrollo de la guía
Esta Guía de Buenas Prácticas ha sido elaborada basándose en el documento creado por la Comisión de Seguridad y Salud de la Agrupación de Fabricantes de Cementos de España, OFICEMEN, con la que se pretende “dar un paso más en el camino de cumplir el objetivo prioritario del sector: la Prevención de Riesgos Laborales.”
Esta Guía de Buenas Prácticas para la Prevención de Riesgos Laborales en el Sector Cementero Español, fue publicada por primera vez en 2008 y es un referente en la industria cementera.
Así, en los siguientes apartados, veremos algunas de las tareas que se realizan en los distintos procesos de fabricación en la industria cementera estructurando cada apartado de la siguiente manera:
- 1.- Introducción.
- 2.- Riesgos específicos.
- 3.- Consecuencias para la salud.
- 4.- Buenas Prácticas en PRL:
- En cuanto al personal.
- En cuanto a las instalaciones, maquinaria y equipos.
Puedes consultar la guia completa en el siguiente enlace: Guía de Buenas Prácticas para la Prevención de Riesgos Laborales en el Sector Cementero Español
Casos prácticos
A continuación, veremos los riesgos, accidentes y las consecuencias específicas de cada tarea, así como las indicaciones de buenas prácticas de Prevención de Riesgos Laborales en cada uno de ellos, que incluyen, entre otros aspectos el uso de Equipos de protección individual, EPIs.
1. Seguridad vial
En cuanto a las medidas de seguridad en materia de Seguridad Vial en las instalaciones cementeras, estos son los aspectos comunes a tener en cuenta en todos los escenarios que comentaremos:
- Mantener una velocidad adecuada dentro y fuera de las instalaciones.
- Estacionar en los lugares habilitados.
- Llevar puesto el cinturón de Seguridad siempre que se esté dentro del vehículo.
- Circular por las instalaciones a velocidad adecuada.
- Estacionar en los lugares acondicionados para ello.
- No realizar arrancadas bruscas ni paradas.
- Marcha atrás con ayuda de señalista.
1.- Introducción
En primer lugar, hay que destacar que los accidentes viales laborales pueden clasificarse en dos grupos principales:
- Accidentes “en misión”: los que se producen durante la jornada laboral por la tipología del puesto de trabajo o circunstancias del mismo como transporte de pasajeros, desplazamientos a visitar clientes, personal de maquinaria de construcción, etc.
- Accidentes “in itínere”: los que se producen desde el domicilio del trabajador a su puesto de trabajo.
2.- Riesgos asociados
- Los desplazamientos de entrada y salida de los trabajadores, visitantes, etc.
- La entrada de vehículos de transporte de materias primas y equipamiento de pequeño, medio y gran tonelaje.
- La salida de vehículos de distribución del producto terminado tanto a granel como ensacado.
- Los desplazamientos internos del personal para realizar sus labores, trasladarse a vestuarios, comedores, enfermería, vigilacia, etc.
- Colisiones entre vehículos.
- Colisiones de vehículos contra objetos estáticos, como tuberías, material de obra, muros, etc.
3.- Consecuencias para la salud
- Golpes de distinta gravedad.
- Esguinces cervicales.
- Fracturas.
- Hemorragias.
- Fallecimiento.
4.- Buenas prácticas en PRL
a) En cuanto al personal:
- No permitir el acceso a las instalaciones de personas ni vehículos que no tengan autorización.
- Proporcionar en el control de accesos información sobre las medidas de seguridad vial internas en las instalaciones de la fabrica.
- Tanto los trabajadores como los visitantes a la fabrica, deberán portar prendas de alta visibiliad, como chalecos reflectantes.
- En los traslados por la fábrica y sus instalaciones, los peatones deberán usar obligatoriamente las aceras.
- Los trabajadores solo podrán circular a pie por aquellas áreas en que esté permitido y no sean de uso exclusivo de vehículos.
- Prestar especial atención cuando haya vehiculos circulando por donde camina, evitando colocarse en su trayectoria, o en zonas donde la visibilidad del conductor sea nula o reducida.
- Uso de EPIs que incluyan casco y ropa reflectante.
b) En las instalaciones y máquinas:
- Establecer controles de acceso, para la entrada y salida y de personas y medios de transporte.
- La ubicación del parking para el personal, vestuarios, oficinas, enfermeria, y todo espacio susceptible de ser recorrido por viandantes, debe ser diseñada de forma que los desplazamientos sean los menores posibles entre dichas zonas.
- Las zonas en que se produzcan maniobras de vehículos pesados condicionaran la circulacion del resto de vehículos, trabajadores y visitantes en la empresa.
- El recinto debe tener la señalización, horizontal y vertical suficiente para poder gestionar correctamente la circulación y, de esta manera, garantizar la seguridad en el interior de las instalaciones
- Para evitar aumentos de velocidad indeseados y aumentar la eficacia de las señales de velocidad, deben construirse badenes en puntos sensibles.
- Los sentidos de la circulacion de vehiculos deben ser únicos
- El recinto debe tener aceras y pasos de peatones, señalizadas horizontal y verticalmente
- Los vehiculos y la maquinaria deben estar en perfecto estado de matenimiento
- Los dispositivos de protección deber estar activados
- El vehiculo debe contar con todos los permisos correspondientes tanto para circular por la cantera como para transportar mercancias.
- Respetar en todo momento la señalización y las normas del código de circulación.
2. Cargues de cemento a granel
1.- Introducción
El cemento, una vez terminado su proceso de fabricación, puede ponerse a la venta en sacos o a granel, mediante camiones cisterna que se cargan en ellos desde tolvas o silos.
La Guía de Buenas Prácticas para PRL en el sector cementero, nos indica, a modo de ejemplo:
“Para poder cargar el cemento el trabajador ha de subirse necesariamente a la cisterna del camión para proceder a la apertura de las tapas. Las cisternas tienen una altura media de cuatro metros y, por lo general, no disponen de protección perimetral. Estos son dos de los problemas más importantes que debemos afrontar.
A estos riesgos hay que añadir las escasas medidas de seguridad de los camiones cisterna. Estos camiones, por lo general, disponen de accesos a través de escalas a la parte superior del camión, donde se encuentran las tapas para el llenado. Los problemas anteriores se agravan en el caso de condiciones climatológicas adversas como pueden ser la lluvia y el hielo.
El cargue de cemento comprende todo el proceso desde que el camión entra en las instalaciones hasta que abandona las mismas con el producto cargado.”
2.- Riesgos específicos
- Accidentes de trafico con el camión cisterna.
- Riesgo en la apertura y cierre de forma mecanica de la tapa de la cisterna.
- Participación en la operativa de personal ajeno a la empresa no formado en su politica de PRL.
- Caida de particulas y material en el momento de la carga.
- Inhalación de polvo y gases de combustión.
- Atropellos.
- Vibraciones excesivas .
- Ruido de alta intensidad.
- Caída a distinto nivel en las cisternas.
- Inhalación de polvo y gases de combustión.
- Vibraciones y ruidos de alta intensidad.
3.- Consecuencias para la salud
- Golpes de distinta gravedad.
- Daño en el sistema auditivo.
- Fracturas.
- Problemas musculares: Esguinces Distensiones Torceduras.
- Intoxicación.
- Fallecimiento.
4.- Ejemplos de buenas prácticas
La descarga a cisternas desde silos o tolvas deben ser realizadas exclusivamente por personal formado y con experiencia.
a) En cuanto al personal:
- Nombrar y formar un jefe de maniobra.
- Planificar adecuada y diariamente el trabajo en cuanto a número de operaciones.
- Informar a todo el personal.
- Vigilar la existencia de personas y vehículos en el radio de acción.
- Subir y bajar frontalmente las escalas a la cisterna.
- El conductor del camión y el personal de la planta deben estar presentes dure toda la manobra y mantener distancias de seguridad con las máquinas.
- Utilización de EPIs que incluyan: casco, mascarillas, protectorse auriculares, ropa reflectante, guantes, fajas y calzado de seguridad.
b) En las instalaciones, máquinas y equipos:
- Los accesos a las tolvas o silos deben tener una base firme que soporte el peso de los camiones cisterna.
- Los accesos deben ser en llano y estar libres de materiales que dificulten el movimiento y maniobras del vehículo.
- Los espacios de carga deben estar situados en lugares próximos a las vías y tener suficiente espacio para que el vehículo estacione sin obstruir entradas o salidas.
- La boca de descarga debe estar lo más cerca posible de donde se estaciona el vehículo para que las mangueras de conexión cumplan con la longitud permitida por las normativas al respecto.
- El silo de almacenamiento o la tolva, deben tener un sistema de filtros que evite las emisiones de polvo de cemento a la atmósfera y dispositivos de ventilación que prevengan los daños que puede producir la presurización del cemento al ser descargado en el vehículo.
- Definir claramente el área de trabajo, circulación vehículos, personas, etc.
- Señalizar accesos, riesgos y áreas de trabajo con prohibiciones de paso.
- Coordinación de maniobras reservando una zona de seguridad alrededor de toda la maquinaria.
- Que el espacio de trabajo sea adecuado, con la amplitud suficiente y libre de obstaculos como tuberías, líneas eléctricas, etc.
- Mantener los vehículos en perfecto estado, con su documentación en regla y debidamente señalizado.
- Medidas ATEX.
3. Carga y transporte de materiales en cantera
1.- Introducción
Recordemos que en este proceso se extraen de la cantera las materias primas que se cargan con maquinaria pesada para ser trasladada a las tolvas de las trituradoras.
Las operaciones de carga de materiales en la cantera, se realizan con retroexcavadoras y palas cargadoras que suelen ir montadas sobre orugas, lo que reduce su capacidad de traslación, y las de transporte con camiones de gran tamaño o dúmperes.
Se consideran operaciones de alto riesgo por lo que es imprescindible una buena política empresarial de PRL.
En una cantera existe movimiento de tierras y de maquinaria pesada, por esta razón se deben extremar las medidas preventivas ya que una mala acción puede provocar un accidente mortal.
2.- Riesgos específicos
- Proyecciones de partículas durante la carga de camiones.
- Colisión de maquinas.
- Golpes, atrapamientos y aplastamientos.
- Exposición a altas temperaturas.
- Incendios y explosiones.
- Atropellos.
- Volcado de maquinaria.
- Polvo en suspension.
- Ruido de alta intensidad.
- Vibraciones.
3.- Consecuencias para la salud
- Golpes.
- Problemas muculares.
- Fracturas.
- Intoxicación.
- Daños en el sistema auditivo.
- Quemaduras y golpes de calor.
- Fallecimiento.
4.- Ejemplos de buenas prácticas
a) En cuanto al personal:
BUENAS PRÁCTICAS | |
---|---|
Formar y nombrar un jefe de cantera. | Formar y nombrar un coordinador de maniobras. |
Mantener informado a todo el personal. | Mantener distancias de seguridad con las maquinas. |
No permanecer innecesariamente en el exterior del vehiculo. | No pasar por debajo de los cazos de las excavadoras. |
No acercarse a bordes de taludes, pistas, etc. | Subir y bajar frontalmente de los vehículos. |
EPIs específicos:
EQUIPOS DE PROTECCIÓN INDIVIDUAL | |
---|---|
Casco de seguridad. | Mascarilla para evitar el polvo. |
Protectores auriculares. | Ropa reflectante. |
Guantes y fajas antivibraciones. | Calzado de seguridad. |
b) En las instalaciones, máquinas y equipos:
- Definir claramente las área de trabajo. de circulación vehículos, de trásito de personas, etc.
- Vigilar permanentemente la existencia de personas en el radio de acción de los vehículos.
- Establecer zonas de seguridad alrededor de toda la maquinaria.
- Evitar que la construcción tenga pendientes pronunciadas.
- Asegurar que el firme esté siempre libre de obstáculos o materiales (líneas eléctricas, tuberías, subterráneas o aéreas, etc…).
- Señalizar accesos, riesgos y áreas de trabajo con prohibiciones de paso.
- Colocar donde sea posible barandillas de seguridad o en su defecto utilizar arnes en alturas superiores a 2 m.
- Regar las zonas de trabajo.
- Utilizar vehiculos con cabina para minimizar aspiración polvo, aislar ruido y proteger en caso de vuelco.
- Tener los vehiculos en perfecto estado de mantenimiento.
- NO anular ningún dispositivo ni protección.
- Calzar las ruedas de los vehiculos mientras realizan las operaciones.
4. Trabajos en altura con plataforma elevadora
1.- Introducción
En algunos trabajos de mantenimiento, reparación o inspección en las instalaciones, se utilizan plataformas elevadoras que proporcionan una mayor rapidez de instalación que los andamios tradicionales.
Los accidentes que se producen en la realización de trabajos en altura son de elevada gravedad.
Se entiende como trabajos en altura a todos aquellos que se realizan a una altura superior a 2m o menor si así lo consideran los responsables de la instalación del andamio.
Para eliminar estos riesgos, las plataformas elevadoras deben emplearse de forma adecuada, teniendo en cuenta el firme de la zona en que se coloca y coordinando los trabajos con el resto de operaciones que se realicen en la misma zona.
2.- Riesgos específicos
- Caídas a distinto nivel, al mismo nivel, o en altura desde la plataforma.
- Caída de materiales sobre personas por desplome, derrumbe o desprendimiento.
- Riesgo del operario de sufrir golpes, choques o atrapamientos.
- Riesgo por desplazamiento de la plataforma contra personas y equipos fijos o móviles.
- Aprisionamiento de operarios por caidas entre alguna de las partes de la estructura o entre ésta y la propia plataforma.
- Aprisonamiento o aplastamiento por vuelco de la plataforma.
- Incendio o explosión.
3.- Consecuencias para la salud
- Golpes de distinta gravedad.
- Traumatismos severos.
- Fracturas.
- Quemaduras y golpes de calor.
- Fallecimiento.
4.- Buenas Prácticas en PRL
En los trabajos en altura con plataforma elevadora, hay que tener especial cuidado con:
- Las condiciones meteorológicas.
- No elevar cargas voluminosas.
- No sobrepasar la carga máxima.
a) En cuanto al personal:
- Nombrar y formar un jefe de maniobra.
- Vigilar la existencia de personas y vehículos en el radio de acción.
- Utilización de la plataforma solo por personal formado y con experiencia.
- Actualizar las normas de PRL a los operarios, en especial de las medidas de seguridad relativas a trabajos en altura.
- Los trabajadores solo podrán circular a pie por aquellas áreas en que esté permitido y no sean de uso exclusivo de vehículos.
- Subir y bajar de la plataforma solo cuando esté al nivel del suelo y siempre por laparte exterior.
- No sujetarse ni anclarse a estructuras fijas.
- No saltar sobre la plataforma ni desde ella.
- Utilizar los EPIs general de protección y un arnés anclado de forma segura a un punto fijo de la plataforma.
b) En las instalaciones, máquinas y equipos:
- Definir claramente el área de trabajo, circulación vehículos, personas, etc.
- Señalizar accesos, riesgos y áreas de trabajo con prohibiciones de paso.
- Coordinación de maniobras reservando una zona de seguridad alrededor de toda la maquinaria.
- Mantener distancias a otros trabajos.
- Señalizar y aislar las líneas eléctricas.
- Asegurar el firme en que se asiente la plataforma.
- Ayudarse de un señalista si la visibilidad es limitada.
- Mantener el perímetro libre de obstaculos en superficie o aereos, y de tránsito de vehiculos y personas.
- La plataforma debe tener, preferiblemente, un pasillo metalico en su parte superior, limpio de obstaculos, con barandilla o linea de vida.
- Mantener la plataforma en perfecto estado de mantenimiento.
- Protocolo ATEX antiincendios.
5. Trabajos con andamios
1.- Introducción
El Instituto Nacional de Seguridad e Higiene en el Trabajo, publica en su nota técnica de prevención, NTP, sobre “Andamios tubulares de componentes prefabricados (I): normas constructivas.” la siguiente descripción de los andamios:
- “Los andamios de trabajo prefabricados, sistema modular, son estructuras tubulares provisionales para proporcionar un lugar de trabajo, de paso, o de protección seguro para la construcción, mantenimiento, reparación o demolición de edificios, entre otros. Según se haya definido su uso, los andamios pueden cumplir la función de habilitar superficies de trabajo, sustentación de carga, protección horizontal o perimetral, de servicio (para circulación de operarios y materiales conectando diferentes zonas), etc.”
Los accidentes que se producen en la realización de trabajos en altura son de elevada gravedad.
Se entiende como trabajos en altura a todos aquellos que se realizan a una altura superior a 2m o menor si así lo consideran los responsables de la instalación del andamio.
Al igual que sucede con el uso de plataformas elevadoras, para eliminar riesgos, los andamios deben emplearse de forma adecuada, teniendo en cuenta el firme de la zona en que se coloca y coordinando los trabajos con el resto de operaciones que se realicen en la misma zona.
2.- Riesgos específicos
- Caídas a distinto nivel en altura desde el andamio o a través de las trampillas de acceso a otros niveles o pisos.
- Caidas entre plataformas por dejar abiertas las trampillas de acceso a ellas.
- Caída de materiales sobre operarios por desplome, desprendimiento.
- Desplome de la estructura.
- Riesgo del operario de sufrir golpes, choques o atrapamientos.
- Riesgo por desplazamiento o caida del andamio o alguna de sus partes sobre personas y equipos fijos o móviles.
- Vuelcos de la estructura con peligro de aprisonamiento o aplastamiento.
- Anclaje inadecuado de los arneses de seguridad a puntos no seguros o adecuados.
- Accidentes por mal uso de las escalas de acceso a las distintas plantas de la estructura del andamio.
- Rotura de las plataformas de trabajo por sobrecarga, deterioro de las garras o de la superficie.
- Accidentes durante la elevación o descenso materiales.
- u otros elementos al utilizar medios inadecuados.
- Tropiezos con materiales, cordajes y herramientas.
- Peligro de incendio o explosión por proximidad a líneas eléctricas de alta tensión o baja tensión aéreas o en fachada.
3.- Consecuencias para la salud
- Golpes.
- Traumatismos severos.
- Fracturas.
- Quemaduras.
- Fallecimiento.
4.- Buenas prácticas en PRL
a) En cuanto al personal
Los andamios solamente pueden ser montados, desmontados o manipulados bajo la dirección y ejecución de una persona habilitada con formación/experiencia por la legislación.
- Evitar que las personas caigan o estén expuestas a caídas de objetos.
- Prohibir la manipulación de cualquier elemento que forme parte del andamio.
- Los operarios deben tener especial cuidado de no dejar ningún tipo de carga, herramienta u material sobre los andamios.
- Ningún operario puede HACER Y USAR plataformas de trabajo improvisadas.
- Todas las personas implicadas en un proceso en el que se requiera el uso de un andamio debe estar permanente formada en detección de incidencias, forma de proceder en caso de detectar deficiencias, señalizaciones, anulación de andamios, etc….
- Acceder al andamio por el lugar habilitado para ello y no escalando verticalmente la estructura.
- Mantener en todo momento las distancias de seguridad entre barandillas y plataforma.
- Revisión diaria del equipo EPI anticaída.
- Mantén el ORDEN Y LIMPIEZA en las plataformas para evitar golpes y resbalamientos.
b) En las instalaciones, máquinas y equipos
En función del tipo de andamio que va a instalarse, este deberá tener un plan de montaje específico proporcionado por el fabricante.
Los andamios deberán obligatoriamente ser inspeccionados por personas habilitadas legalmente para tal fin:
- a) Antes de su puesta en servicio.
- b) A continuación, periódicamente.
- c) Tras cualquier modificación, período de no utilización, exposición a la intemperie, sacudidas sísmicas, o cualquier otra circunstancia que hubiera podido afectar a su resistencia o a su estabilidad.
Una vez terminada la construcción del andamio y realizada la correspondiente inspección, se procederá a su certificación.
- Instalar barandillas de seguridad en todas las zonas de trabajo.
- Todas las operativas de montaje, desmontaje o manipulación deberán estar recogidas en una instrucción interna de aplicación.
- Documentación y certificaciones actualizadas y disponibles.
- Inspecciones periodicas de los andamios.
- Utilizar siempre materiales exentos de cualquier anomalía que afecten a su comportamiento, como tubos deformados.
- Proteger los elementos de apoyo contra el riesgo de deslizamiento.
- La estructura no deberá tener vacios peligrosos.
- El andamio debe ser apropiado al tipo de trabajo que se va a realizar y adecuado al peso que deban soportar.
- El número de trabajadores que vayan a utilizarlo debe ser cuidadosamente calculado y coordinado.
En los trabajos en altura con andamio, hay que tener especial cuidado con:
- Tener en cuenta condiciones meteorológicas.
- No elevar cargas voluminosas.
- No sobrepasar la carga máxima.
6. Limpieza de torre de ciclones
1.- Introducción
La limpieza de torres de ciclones se realiza a temperaturas muy elevadas, lo que puede producir accidentes de importante gravedad, sobre todo los relacionados con el contacto de los trabajadores con el material caliente.
La torre de ciclones es el lugar en el que se centrifuga y decanta el material primario para convertirlo en Clinker, mediante corrientes de aire rotativas, transformándolo en partículas que caen por gravedad y que posteriormente entraran en un horno para continuar con el proceso de transformación en cemento.
En ella deben realizarse periódicamente tareas de mantenimiento y reparación y ocasionalmente de desatasco.
En el caso de desatasco, la tarea es realizada por al menos dos personas, una al frente de la lanza de agua y otra frente al equipo de alta presión.
Estas tareas se realzan mediante mangueras a alta presión, que exponen a los trabajadores a riesgos como quemaduras, impactos por proyección de partículas y cortes e incluso seccionamiento de miembros por la presión de las lanzas de agua.
La limpieza tradicional se realiza de manera manual con sistemas de aire o agua y, en algunas ocasiones mediante la introducción de una carga explosiva (o de CO2) en el interior del ciclón que se denominan sistema Cardox.
En la primera inspección de la maquinaria, hay que tener muy en cuenta el riesgo de desprendimiento del material adherido en las paredes y valor la posibilidad de retirar las incrustaciones con medios mecánicos.
Inicialmente se realizará una inspección teniendo en cuenta que debemos protegernos contra el riesgo de desprendimiento de material adherido de las paredes, con lo que deberá estudiarse si es posible realizar la retirada de incrustaciones con medios mecánicos.
Esta labor tiene algunas especificaciones, que deben tenerse en cuenta antes de su inicio y que según nos indica la Guía son:
- La limpieza se realizará siempre de abajo hacia arriba. Esto quiere decir que se limpiará primero la parte inferior del ciclón y luego la superior, ya que, si se hiciese al revés, no se desharía el atasco.
- Se procederá a la comprobación de que todos los puntos en los que ha rebosado el material del ciclón ha sido enfriados con agua abundante.
Antes de empezar el trabajo, deberá realizarse:
- La limpieza y purgado de acceso antes de entrar en el mismo.
- Retirar el magnetotérmico de motor eléctrico.
- Se anularán todos los cañones de aire.
- Se bloqueará el ascensor en el nivel superior/inferior (cada instalación determinará el nivel en que quiere bloquear el ascensor) señalizando la prohibición de su utilización.
- Se mantendrá la torre en depresión.
- Los trabajos en el interior, deberá utilizarse una plataforma que cubra la totalidad del hueco, que resista el peso del personal, materiales, deformaciones por temperatura o caídas.
- Se procederá a la comprobación de que todos los puntos en los que ha rebosado el material del ciclón han sido enfriados con agua abundante y están señalizados.
2.- Riesgos específicos
- Contacto con material caliente fino y a muy alta temperatura (hasta 800 ºC) que fluye como el agua y se desplaza a gran velocidad , pudiendose introducir en cualquier parte, provocando graves quemaduras a los trabajadores.
- Golpes por fragmentos y pegaduras de material o incrustaciones desde paredes y techo.
- Golpes y cortes por desgaste de chapas.
- Cortes o seccionamientos de extremidades por utilización de herramientas de alta presión.
- Atmósfera insalubre por el espacio de trabajo reducido y con aberturas limitadas que puede provocar asfixia.
- Incendios y explosiones.
- Estrés térmico.
3.- Consecuencias para la salud
- Golpes.
- Traumatismos severos y seccionamientos.
- Fracturas.
- Intoxicación.
- Asfixia.
- Quemaduras y golpes de calor.
- Fallecimiento.
4.- Buenas prácticas en PRL
De forma general, para evitar riesgos al limpiar torres de ciclones, es fundamental que estas labores sean realizadas por personal especializado y que los trabajadores sigan los procedimientos específicos tanto en las labores de limpieza como en las de mantenimiento e inspección.
a) En cuanto al personal
- Informar a todo el personal de las medidas de prevención.
- Realización de tareas solo por personal capacitado, formado y con experiencia.
- Prohibición de acceso al resto de personal a la zona de seguridad.
- Planificación y cumplimiento de los tiempos de descanso e hidratación.
- Uso obligatorio del arnés con cuerda de salvamento desde el exterior.
- Revisión diaria del equipo EPI.
Equipos de protección individual
- Casco de seguridad.
- EPI’s ignífugos adicionales (guantes, peto capuchón, cubrebotas, ...).
- Arnés de salvamento anclado a punto fijo.
b) En las instalaciones, máquinas y equipos
- Mantener personal de vigilancia permanente.
- Definir claramente las áreas de trabajo, circulación vehículos, personas…
- Mantener distancias a otros trabajos.
- Señalizar accesos, riesgos y áreas de trabajo con prohibiciones de paso.
- Refrigerar el ambiente antes de entrar en las torres.
- Colocar candados con señalización en los puntos de corte de corriente, tuberías, circuitos hidráulicos, agua, aire, etc. que puedan suponer riesgo por una puesta en marcha intempestiva.
- Eliminar llamas, superficies calientes, chispas, chispas de origen mecánico y/o eléctrico, descargas electrostáticas, sobrecalentamientos por fricción mecánica de los materiales eléctricos, motores térmicos, etc.
7. Reparaciones de hornos y enfriadores
1.- Introducción
Antes de comenzar cualquier labor de desatasco o limpieza en los intercambiadores de calor u hornos Clinker, los trabajadores deberán asegurarse del enfriamiento del horno.
Las tareas relacionadas con los hornos y enfriadores incluyen:
- Inspección.
- Mantenimiento.
- Reparación de equipos.
- Picado.
- Encofrado.
- Hormigonado.
- Reparación del refractario.
- Limpieza y reparación de parrillas del horno y del enfriador.
- Limpieza de mecanismos del horno.
En todos los trabajos en los que haya que acceder a los hornos y enfriadores, los trabajadores deben protegerse del riesgo de desprendimiento de material adherido de las paredes, y deberá estudiarse si es posible la retirada de incrustaciones con medios mecánicos, como un robot, en cuyo caso deberán mantenerse distancias de seguridad con respecto al robot y su zona de acción.
Las operaciones manuales sobre incrustaciones y ladrillos comenzarán siempre por la inspección visual de la costra, quitando primero la que parezca comenzar a descomponerse o desprenderse; la retirada se efectuará siempre desde arriba y proseguirá por los laterales. Al tratarse de un operativo manual con uso de barra y macho, deberá realizarse rotaciones de personal suficientes que permitan a los trabajadores hacer descansos y evitar lesiones musculares.
2.- Riesgos específicos
Proyecciones de partículas, fragmentos y materiales incandescentes. | Golpes y atrapamientos por elementos móviles de equipos como giros del horno. |
Golpes y cortes por objetos o herramientas y por desprendimiento de material adherido de las paredes. | Quemaduras por contactos térmicos de altas temperaturas, llamas, calor radiante y material incandescente. |
Electrocuciones por alta o baja tensión. | En los espacios confinados: asfixia por acumulación e inhalación de gases y estrés térmico. |
Explosiones e incendios por acumulación de gases y combustibles. | Incendios y explosiones. |
3.- Consecuencias para la salud
- Golpes y cortes.
- Problemas musculares.
- Fracturas.
- Intoxicación.
- Asfixia.
- Quemaduras y golpes de calor.
- Fallecimiento.
4.- Buenas prácticas en PRL
Como en todas las tareas que implican riesgos graves, todos los intervinientes deben conocer y seguir los protocolos específicos.
a) En cuanto al personal
- Realizar la tarea solo si se cuenta con la formación y experiencia necesaria para ello.
- El encargado de la tarea debe estar en contacto permanente con los operarios.
- Respetar los tiempos de descanso e hidratación para evitar el estrés térmico.
- Utilizar y mantener en buen estado el equipo EPI.
- Revisar periodicamente el anclaje del arnes de salvamento exterior.
Equipos de protección individual
- Casco de seguridad.
- Arnés con cuerda de salvamento desde el exterior.
- Trajes de protección térmica.
b) En las instalaciones, máquinas y equipos:
- Mantener vigilancia y monitorización permanente de la atmosfera del interior de los hornos.
- Garantizar la ventilación del espacio confinado cuando hay operarios en su interior.
- Refrigerar el ambiente antes de la entrada de personas.
- Proveer los hornos de Iluminación antidefragante y portátil.
- Señalizar la presencia de personas en el interior de los hornos y evitar que se realicen tareas dentro del área de seguridad.
- Señalizar accesos, riesgos y áreas de trabajo con prohibiciones de paso.
- Equipo de rescate y primeros auxilios exterior.
- Colocar candados con señalización en los puntos de corte de corriente, tuberías, circuitos hidráulicos, agua, aire, que puedan suponer riesgo por una puesta en marcha intempestiva.
- En los trabajos en el interior del horno o enfriador, deberá utilizarse una plataforma que cubra la totalidad del hueco, que resista el peso del personal, materiales, deformaciones por temperatura o caídas.
- Asegurar el bloqueo de las maquinas antes de proceder.
- Protocolo ATEX.
Atex - Buenas prácticas Atex
- Eliminar llamas, superficies calientes, chispas, chispas de origen mecánico y/o eléctrico, descargas electrostáticas, sobrecalentamientos por fricción mecánica de los materiales eléctricos, motores térmicos, etc.
- Si es necesario realizar trabajos con fuego deberá previamente desgasificarse y limpiarse.
- Si se usan herramientas metálicas u otros utensilios que puedan generar chispas, deberá cubrirse el suelo con una manta especial.
8. Seguridad de máquinas
1.- Introducción
En una planta cementera, conviven un elevado número de tipos de máquinas. Todas conllevan un riesgo con gran capacidad de daño, por lo que es fundamental implementar medidas preventivas no solo en su uso, sino también en su mantenimiento y conservación.
Para mantener la maquinaria en perfecto estado es necesario e imprescindible:
- Realizar mantenimientos correctivos para reparar averías que ya se han producido.
- Realizar mantenimientos preventivos, estableciendo un plan anual de mantenimiento consistente en la revisión y, en su caso, sustitución de piezas susceptibles de desgaste y deterioro progresivo.
Para que el mantenimiento sea lo más eficaz posible y con el menor riesgo, deberá seguirse un protocolo específico de mantenimiento, que incluya:
- Coordinación e información entre intervinientes.
- Intervención sobre elementos móviles de máquina.
- Actuación sobre algún tipo de energía (eléctrica, neumática, hidráulica, etc.) de la máquina.
2.- Riesgos específicos
- Atrapamientos entre máquinas o alguno de sus componentes.
- Accidentes producidos por corrosión, desgaste de las partes rotativas, fatiga de los materiales, daños y deformaciones en las partes internas, suciedad, desviaciones de las condiciones normales de la operación, errores humanos.
- Accidentes por máquinas mal diseñadas o utilizadas, mal insonorizadas, equilibradas, ajustadas o mantenidas.
- Electrocución.
3.- Consecuencias para la salud
- Golpes.
- Traumatismos severos y seccionamientos.
- Fracturas.
- Electrocución.
- Daños en el sistema auditivo.
- Quemaduras y golpes de calor.
- Fallecimiento.
4.- Buenas prácticas en PRL
Antes de comenzar cualquier trabajo relacionado con máquinas, deberá realizarse una reunión entre los intervinientes explicando el trabajo a realizar, los riesgos y las medidas preventivas específicas.
a) En cuanto al personal:
- Deberá nombrase un responsable del trabajo (recurso preventivo) que durante todo el trabajo vigile el cumplimiento de medidas preventivas definidas.
- Seguir las instrucciones específicas del fabricante de la máquina en cuanto a mantenimientos.
- Permanecer alejado de las máquinas y nunca manipular ningún elemento sin autorización.
- Acceder a las maquinas por el lugar habilitado para ello.
- Revisión diaria del equipo EPI anticaída.
- Usar EPIs adecuados y en perfecto estado.
Equipos de protección individual
- Casco de seguridad.
- Guantes y fajas.
- Protectores visuales y acústicos.
- Botas de trabajo.
- EPI’s ignífugos adicionales.
b) En las instalaciones, máquinas y equipos:
- Aislar las máquinas de las redes de alimentación eléctrica, hidráulica o neumática desconectando y bloqueando el interruptor de alimentación eléctrica y las válvulas de entrada de cualquier otra fuente de energía (agua, aire, vapor, etc.).
- Anular las energías residuales, ya sean estas de naturaleza eléctrica, hidráulica, neumática, etc.
- Comprobación de que no hay personas en la zona de peligro.
- Proveer y utilizar SISTEMAS DE BLOQUEO que hagan imposible la puesta en marcha de forma intempestiva.
- No comenzar los trabajos hasta estar completamente seguro de que se ha realizado todas las fases del PROTOCOLO DE BLOQUEO.
- Delimitar y señalizar las zonas de trabajo, colocar balizamientos y señalizaciones de riesgos, prohibición de paso a personal ajeno al mantenimiento y personal trabajando en mantenimiento.
- Revisión diaria del equipo EPI anticaída.
- Solo debe poder conectarse la alimentación a la máquina cuando se hayan quitado todos los candados
- Cuando varios trabajadores estén trabajando en una máquina o instalación, puede utilizarse un dispositivo de bloqueo que permita colocar varios candados en la misma máquina para cada tarea (cada uno con el suyo).
- Para el bloqueo de interruptores o válvulas de alimentación, deben utilizarse candados con una sola llave, que estará en poder del empleado que realiza el trabajo en la máquina.
9. Trabajos en molinos
1.- Introducción
El tipo de molienda que se realiza en una planta cementera está muy influenciado por el tipo de cemento que se pretende producir y, por tanto, de los componentes y aditivos que se añaden, que pueden ser molidos junto con el Clinker, o por separado.
La mayor parte de los molinos producen en un sistema de circuito cerrado en los que la máquina separa el cemento dependiendo de la finura requerida devolviendo la parte más gruesa para molerla de nuevo.
Las labores de mantenimiento y reparación de molinos, se realizan en condiciones de temperaturas extremas por lo que uno de los mayores riesgos es el de permanecer un tiempo excesivo en su interior, algo que es objeto de reclamación de regulación por parte de los trabajadores quienes demandan un cuidadoso análisis de periodos máximos de permanencia que garanticen la seguridad y salud de los operarios.
La gran variedad de tipos de cemento hace que los fabricantes de maquinaria, desarrollen cada vez equipos de molienda más eficaces y seguros, siendo los más habituales:
- Los molinos de bolas en circuito abierto o cerrado.
- Los molinos verticales de rodillos.
- Las prensas de rodillos.
Los trabajos que se realizan en los molinos son, entre otros:
- De reparación.
- De eliminación de atascos.
- De revisión y reemplazo en su caso de piezas como rodamientos, cojinetes, placas y tornillería.
- De inspección del circuito de pulverización de agua.
2.- Riesgos específicos
En esta fase de la producción de cemento, hay que tener muy en cuenta la dificultad de evacuación de personas en estado de inconsciencia.
- Atrapamientos y golpes por equipos en movimiento y bandas transportadoras.
- Posibles caídas a las tolvas de alimentación.
- Exposición a elevados niveles de ruido.
- Exposición a ambientes pulvígenos con riesgo de asfixia.
- Caída de objetos y de personas desde alturas.
- Proyecciones de partículas y fragmentos.
- Golpes y atrapamientos por máquinas y sus componentes.
- Incendios y explosiones cuando los molinos utilizan carbón.
3.- Consecuencias para la salud
- Golpes y cortes.
- Amputaciones.
- Fracturas.
- Intoxicación.
- Daños en el sistema auditivo.
- Quemaduras y golpes de calor.
- Fallecimiento.
4.- Buenas prácticas en PRL
a) En cuanto al personal:
- Nombrar un responsable de maniobras que planifique diariamente el trabajo e informe a todo el personal.
- Prevenir los golpes de calor y mareos respetando los tiempos, descansos e hidratación.
- Permanecer en contacto continuo con el encargado, tanto en tareas exteriores como interiores.
- Llevar colocado siempre un arnés anticaída que facilite la evacuación.
- Acceder subiendo por escaleras adecuadas y con arnés de seguridad amarrado.
Equipos de protección individual
- Casco de seguridad.
- Guantes, gafas y fajas.
- Arnés anticaida.
- Arnés de rescate.
b) En las instalaciones, máquinas y equipos:
- Señalizar para impedir que los trabajadores se acerquen a tres metros de la vertical del molino.
- Realizar mediciones de temperatura, humedad y gases.
- Analizar atmosfera interior y monitorizarla.
- Utilizar alumbrado antideflagrante.
- Mantener permanentemente un equipo de rescate y primeros auxilios exterior.
- Colocar dispositivos luminosos y acústicos.
- Colocar candados y/o placas personales en los puntos de corte de corriente, circuitos hidráulicos, de agua, aire, etc. para impedir un arranque accidental de los equipos.
- Vaciar suficientemente el molino de material.
- Optimizar la ventilación en el interior del molino para minimizar su tiempo de enfriamiento.
- Mantener siempre cerradas las trampillas de entrada en las tolvas.
- Asegurar todos los accesos.
- Protocolo Atex.
10. Atascos en machacadoras
1.- Introducción
Las machacadoras son maquinaria provista de mandíbulas cuyo tamaño y diseño se va adaptando al tipo de grano que se pretende conseguir, atendiendo a necesidades de manejabilidad del producto.
Para producir cemento, uno de los pasos iniciales consiste en reducir, mediante las mismas, los bloques de roca de la cantera para que puedan ser manejados más fácilmente. En este proceso intervienen distintas maquinas a modo de circuito.
En las operaciones de mantenimiento, se valorará inicialmente la utilización de medios mecánicos, como los martillos hidráulicos, para llegar a los elementos en movimiento, evitando manipulaciones manuales. En caso de ser requerida una actuación manual, deberá realizarse siguiendo el protocolo de bloqueo.
En toda la operativa de reducción de tamaño mediante maquinas machacadoras, existe roce entre el material y las partes metálicas de los equipos lo que produce un gran desgaste por abrasión en los componentes de la máquina y una alta probabilidad de deterioro de la misma al poder contener el producto en bruto otros materiales metálicos que no son triturables, producto del arranque de la roca o de su transporte, como barrenas, tornillería, etc.
El diseño de las máquinas de última generación está encaminado a prevenir los atascos mediante la temprana detección de presencia de estos materiales metálicos que pueden provocar, además de deterioro de la máquina, accidentes graves en cualquier punto de la machacadora. Para prevenirlos se instalan detectores de metales y sistemas de separación magnética.
Los condicionantes de peligrosidad para las personas en tareas de desatasco de machacadoras, están ligados a variables como:
- La presencia o no en la instalación de martillo hidráulico.
- El tipo o lugar del atasco.
- La necesidad de situarse encima de la piedra o roca para realizar el desatasco.
Todas las tareas relativas a los atascos en machacadoras, deber estar supervisadas y ser autorizadas por el jefe de planta y se consideran de alta peligrosidad. En algunos casos en que las piedras, por su volumen o por el tipo de atasco, no puedan reducirse con el martillo hidráulico, puede ser necesario el uso de explosivos.
2.- Riesgos específicos
- Atrapamientos y golpes por máquinas y bandas transportadoras.
- Atrapamientos entre rocas y mandíbulas.
- Exposición a elevados niveles de ruido.
- Golpes y heridas por entrar en contacto con piezas móviles como rodillos y poleas.
- Accidentes derivados del uso de martillos hidráulicos.
- Proyecciones de partículas y fragmentos.
- Intoxicación por inhalación de polvo.
- Contactos eléctricos, por instalaciones con protecciones eléctricas defectuosas.
- Aplastamiento por acumulación de material en la zona final de las cintas de alimentación.
3.- Consecuencias para la salud
- Golpes y cortes de gravedad.
- Traumatismos severos y seccionamientos.
- Fracturas.
- Electrocución.
- Daños en el sistema auditivo.
- Fallecimiento.
4.- Buenas prácticas en PRL
a) En cuanto al personal:
- Cerciorarse de que la machacadora, las cintas de alimentación y las cintas transportadoras están paradas.
- Utilizar arnés de seguridad en zonas si protección con riesgo de caída de más de 2 m.
- Mantener la distancia de seguridad respecto a la zona de trituración.
- Los trabajadores deben conocer la señalización de atrapamiento de la máquina, la ubicación de las paradas de emergencia de las cintas, alimentadores y otros equipos, alarmas sonoras, etc…
- Los operarios debes estar resguardados, visualizando la operativa de trabajo en cabinas de control, para evitar exponerse a ruidos, polvo, atrapamientos, contacto con elementos móviles, etc…
- El número mínimo de operarios que realizarán estas operaciones será de dos.
- El operario encargado del martillo hidraúlico, es responsable de mantener al resto de trabajadores fuera del radio de acción de las maquinas.
- Revisión diaria del equipo EPI anticaída.
Equipos de protección individual
- Casco de seguridad.
- Guantes, gafas y fajas.
- Ropa reflectante.
- Arnés anclado a punto fijo de la plataforma.
b) En las instalaciones, máquinas y equipos:
- Delimitar zona de seguridad alrededor de toda la maquinaria.
- Definir área de trabajo, circulación vehículos y personas.
- Poner en marcha dispositivos luminosos y acústicos.
- Instalar sistemas de control de emisión de polvo.
- Regar las zonas de trabajo en las que se generen pulvigenos.
- Para los trabajos en altura, emplear andamios o plataformas estables y resistente a deformaciones por temperatura.
- El cableado eléctrico debe mantenerse en perfecto estado de asilamiento, con toma de tierra y llaves de cierre.
- Los pasillos, escaleras y zonas de circulación de personal deben estar lo más alejados posible de las zonas de riesgo de atrapamientos.
- La grúa de piedra, debe revisarse antes de cada actuación, sobre todo los anclajes y el cordaje para levantar la piedra.
- La cinta de alimentación debe pararse siguiendo el procedimiento de descargo acordado.
- En las zonas en las que hay máquinas en movimiento, como grúas de piedra, deberá instalarse pantalla protectora o, en su defecto, existir una distancia física suficiente.
11. Trabajos en silos y tolvas
1.- Introducción
Todos los procesos de fabricación de cemento, requieren el uso de varios tipos de silos y tolvas para almacenar el material bruto o para alimentar la máquina responsable del proceso: machacadora, molino, horno, etc.
El mantenimiento de silos y tolvas consiste básicamente en la limpieza del material adherido a las paredes y del ambiente pulvígeno que se genera durante su uso y el desatasco de tuberías o rotura de algún elemento de la instalación además de la inspección y en su caso reparación de los sistemas de fluidificación.
Frecuentemente los trabajadores deben afrontar el trabajo sobre taludes inestables de gran altura y en espacios limitados en los que materiales en grandes bloques han quedado adheridos a las paredes. En ambos escenarios hay un alto peligro de enterramiento. Estas tareas, desde hace pocos años, se pueden realizar por medios mecánicos sin poner en riesgo la vida de personas.
Para acceder al silo por la parte superior se usan trampillas que deben permanecer cerradas para evitar caídas. La limpieza de estas instalaciones debe realizarse de arriba abajo, utilizando arnés de seguridad. En ocasiones se utilizan lanzas de aire.
La Guía nos indica que:
“Antes de iniciar la operativa, deberá estudiarse si es posible realizarla con medios mecánicos, con un sistema de rotación de brazo articulado y accionamiento neumático, o mediante un tubo de aspiración, disparo de proyectiles, o aplicando dióxido de carbono en frio, para evitar tener que acceder a su interior.”
2.- Riesgos específicos
- Explosiones o incendios por presencia de materiales combustibles en el interior del silo.
- Axfisias por ausencia de oxigeno suficiente en espacios reducidos.
- Enterramientos por derrumbe de taludes de material acumulado.
- Accidentes por mala manipulación de los conectores de los cañones de aire de la instalación.
- Golpes por desprendimiento de material adherido a las paredes.
- Golpes por movimientos de material inesperados por obstrucción de los conductos que envían el material a los hornos.
- Inhalación de sustancias toxicas residuales.
- Asfixia por falta de oxígeno.
- Estrés térmico.
3.- Consecuencias para la salud
- Golpes y Cortes.
- Ahogamientos y asfixia.
- Trastornos respiratorios.
- Golpes de calor y desmayos.
- Fallecimiento.
4.- Buenas prácticas en PRL
a) En cuanto al personal:
Antes de realizar cualquier trabajo en el interior de silos o tolvas, es imprescindible verificar los niveles de oxígeno en el interior y la ausencia de gases tóxicos.
- Ninguna persona debe el introducirse en el interior de silos y tolvas innecesariamente.
- Ninguna persona debe introducirse en el interior de silos y tolvas antes de haber agotado todos los medios mecánicos para resolver un atasco.
- Los descensos y los trabajos en el interior de silos y tolvas, solo podrán efectuarse en presencia de un jefe de equipo que vigile la tarea sin acceder al silo personalmente y no abandone el puesto de vigilancia por ninguna circunstancia.
- Utilización de arnés de seguridad y elementos de protección en perfecto estado de mantenimiento.
Equipos de protección individual
- Arnés con anclaje y cuerda de salvamento.
- Casco de seguridad.
- EPI’s ignífugos adicionales (guantes, peto capuchón, cubrebotas).
- Mascarillas especiales.
b) En las instalaciones, máquinas y equipos
Antes de empezar el trabajo, deberá realizarse:
- Parada y bloqueo las instalaciones de llenado y vaciado, colocando bridas ciegas.
- Limpieza y purgado antes de acceder a interiores.
- Anulación de los cañones de aire, cortando la entrada de aire y disparándolos manualmente para descargarlos, y desconectarlos eléctricamente.
Buenas prácticas
- Prohibir permanecer en o bajo canales de vaciado durante los trabajos de limpieza.
- Dotar la instalación de medios mecánicos que eviten la intervención de personas.
- Señalizar accesos, riesgos y áreas de trabajo con prohibiciones de paso con señales luminosas y acústicas y especialmente con avisos de “No conectar. Personal trabajando”.
- Instalar elementos de ventilación forzada.
- Dotar la instalación con sistemas de refrigeración del ambiente.
- Asegurar una buena iluminación.
- Equipo de rescate y primeros auxilios exterior.
- Colocar candados con señalización en los puntos de corte de corriente, tuberías, circuitos hidráulicos, etc. que puedan suponer riesgo por una puesta en marcha intempestiva.
- Descargar y cortar eléctricamente las salidas de los cañones de aire.
- Parar y bloquear las instalaciones de llenado y vaciado, e instalar en los conductos de entrada bridas ciegas.
- Asegurar que los accesos se cierran cada vez que se interrumpa el trabajo.
- Protocolo antiincendios.
12. Cintas transportadoras
1.- Introducción
Las cintas transportadoras son elementos auxiliares que reciben materiales y los conducen a otro punto de la instalación.
Por lo general no requieren que un trabajador opere sobre ellos de forma continua.
Pueden ser fijas o móviles y normalmente, son elementos de sencillo funcionamiento que producen una muy baja frecuencia de problemas mecánicos, y cuyo componente básico es una banda flexible, que se desplaza sobre rodillos, montada sobre un bastidor metálico que le proporciona soporte. Suelen ser regulables en cuanto a su altura y su ángulo de inclinación.
Los trabajos de mantenimiento que se realizan en ellas suelen ser de inspección, limpieza, centrado, cambio o reparaciones en la banda y lubricación.
2.- Riesgos específicos
- Atrapamiento de personas por partes móviles de la máquina.
- Riesgo por contacto eléctrico.
- Caída de personas desde o sobre la cinta.
- Golpes por desprendimiento de materiales transportados.
- Riesgo de inhalación de polvo en las proximidades de la cinta.
3.- Consecuencias para la salud
- Golpes y cortes.
- Electrocución.
- Fracturas.
- Intoxicación.
- Daños en el sistema auditivo.
- Quemaduras y golpes de calor.
- Fallecimiento.
4.- Buenas prácticas en PRL
a) En cuanto al personal
- Las operativas de mantenimiento y desatasco deberán realizarse por personal capacitado, formado y autorizado de la empresa, nombrando un encargado de la operativa.
- Prohibir la manipulación en la proximidad de los tambores, con la cinta en marcha.
- Ningún operario puede HACER Y USAR plataformas de trabajo improvisadas.
- Mantener en todo momento las distancias de seguridad entre barandillas y plataforma.
Equipos de protección individual:
- Casco de seguridad.
- Calzado de seguridad.
- Mascarillas filtrantes.
- Protección auditiva.
b) En las instalaciones, máquinas y equipos
- En instalaciones interiores de minería o en lugares donde puede haber gases, instalar detectores continuos de gases.
- Señalizar y balizar el área de actuación para prohibir el acceso a la zona a todo personal ajeno a la operativa.
- Instalar mallas metálicas y protecciones fijas para eliminar el riesgo de atrapamiento en los tambores y rodillos de la cinta.
- Instalar en las cintas mecanismos de parada de emergencia.
- Las cintas trasportadoras dispondrán de pantallas protectoras debajo de los tramos en que la cinta recorra zonas de trabajo o paso.
- En cintas que circulen en altura más de dos metros de altura, instalar plataformas de visita y pasarelas de acceso, ambas con barandilla.
13. Trabajos eléctricos
1.- Introducción
Los trabajos eléctricos pueden realizarse en dos tipos de instalaciones:
- De baja tensión: aquellas cuyas tensiones nominales son iguales o inferiores a 1.000 V, para corriente alterna y 1.500 V para corriente continua.
- De alta tensión: aquellas cuyas tensiones nominales sean superiores a 1.000 V para corriente alterna y 1.500 V para corriente continua.
Puede ser necesario la realización de trabajos de mantenimiento o reparaciones en seccionadores o interruptores, transformadores, condensadores, alternadores, motores, etc….
2.- Riesgos específicos
Las operaciones y trabajos realizados con riesgo eléctrico requieren la aplicación de unas técnicas y procedimientos de trabajo y una formación específica por parte de los trabajadores, dada la gravedad de los daños que pueden ocasionarse por contacto eléctrico.
- Contacto eléctrico directo con elementos en tensión.
- Contacto indirecto con elementos accidentalmente puestos bajo tensión.
- Electrocución por contacto eléctrico (asfixia, quemaduras, fibrilación ventricular e incluso la muerte).
- Incendio por cortocircuito o sobrecarga.
3.- Consecuencias para la salud
- Golpes y caidas.
- Problemas musculares.
- Fracturas.
- Electrocución.
- Quemaduras.
- Fallecimiento.
4.- Buenas prácticas en PRL
a) En cuanto al personal:
El Jefe de trabajo deberá velar por el cumplimiento de las medidas de seguridad y determinar la viabilidad del trabajo.
- Deberá nombrase un responsable del trabajo (recurso preventivo) que durante todo el trabajo vigile el cumplimiento de medidas preventivas definidas.
- Permanecer alejado de las máquinas y nunca manipular ningún elemento sin autorización sin la debida coordinación y autorización.
- Los trabajadores deberán disponer de un apoyo sólido y estable, manos libres, iluminación adecuada y no llevarán objetos conductores, tales como pulseras, relojes, cadenas o cremallera metálicos.
- Informar a los trabajadores directa o indirectamente implicados, de los riesgos existentes, la situación de los elementos en tensión, los límites de la zona de trabajo y cuantas precauciones y medidas de seguridad deban adoptar para no invadir la zona de peligro, comunicándoles, además, la necesidad de que ellos, a su vez, informen sobre cualquier circunstancia que muestre la insuficiencia de las medidas adoptadas.
- Revisión diaria del equipo EPI anticaída.
Equipos de protección individual
- Casco de seguridad.
- EPI’s ignífugos adicionales.
- Fajas y protectores acústicos.
- En altura: Arnés con anclaje a punto fijo.
b) En las instalaciones, máquinas y equipos
- Toda instalación será considerada bajo tensión, mientras no se compruebe lo contrario con el equipo destinado al efecto.
- Identificación exhausitiva de la instalación o conductores en los que se debe efectuar los trabajos.
- Delimitación del trabajo, colocar balizamientos y señalizaciones de riesgos, prohibición de paso a personal ajeno al mantenimiento y personal trabajando en mantenimiento.
- No se utilizarán escaleras metálicas cuando se trabaje en instalaciones eléctricas.
- Para restablecer el servicio al finalizar el trabajo, deberá verificarse que no existen trabajadores en esa instalación y se retirarán las medidas de protección adoptadas. Una vez hechas estas comprobaciones se podrá conectar la tensión nuevamente.
- Señalizar las zonas de peligro de los elementos que permanezcan en tensión, mediante la colocación de pantallas, barreras, envolventes o protectores aislantes cuyas características (mecánicas y eléctricas) y forma de instalación garanticen su eficacia protectora.
- Limitar al máximo número de elementos en tensión.
14. Almacenamiento de productos químicos
1.- Introducción
Todo trabajo que requiera el uso de productos químicos, exige una cuidadosa manipulación de los mismos, debido a los riesgos específicos de estos materiales peligrosos.
Por lo general, los trabajadores en laboratorios de la industria cementera, son rigurosos en la aplicación de las medidas de seguridad. A pesar de esto los accidentes ocasionales que se producen en los laboratorios suelen producirse por no emplear los equipos de protección individual.
Las tareas más concurrentes en los laboratorios de esta industria son:
- Preparación de muestras.
- Análisis químicos.
- Trabajo con sustancias químicas.
Para todas estas tareas, se utiliza una pequeña cantidad de producto químico, por lo que el producto sobrante debe almacenarse en unas condiciones específicas.
Uno de los retos de este sector es la búsqueda de reactivos que causen riesgos más bajos, algo que hoy por hoy, todavía no es una alternativa real.
Cabe destacar que, hasta el momento actual, no se ha producido ningún accidente de gravedad en laboratorios de la industria cementera, al menos ninguno que haya precisado de evacuaciones masivas o haya generado nubes tóxicas.
2.- Riesgos específicos
- Explosiones que generen nubes tóxicas.
- Inhalación de sustancias químicas peligrosas e intoxicación.
- Contacto térmico con sustancias abrasivas.
- Relajación de las medidas de prevención por poca conciencia de riesgo.
3.- Consecuencias para la salud
- Golpes y cortes.
- Intoxicación.
- Quemaduras.
- En raras ocasiones: fallecimiento.
4.- Buenas prácticas en PRL
a) En cuanto al personal
- Todo el personal que trabaje en los almacenamientos de productos químicos debe haber recibido la formación adecuada, conocer con exactitud los procedimientos e instrucciones de trabajo establecidos, contar con las autorizaciones o permisos pertinentes en función de las operaciones que van a realizar.
- Usar protecciones individuales adecuadas.
- Permitir el acceso a este área solo al personal autorizado.
- No fumar ni producir chipas o llamas en zonas de almacenamiento.
- Mantener orden y limpieza.
b) En las instalaciones, máquinas y equipos
En este caso, el foco de los protocolos de prevención se basa en dos áreas principales: manipulación y almacenamiento
Manipulación de productos químicos
- Identificar los riesgos a partir de sus símbolos.
- Usar protecciones individuales adecuadas.
- Respetar las consignas de manipulación y utilización de los productos.
- Usar los productos dentro de recipientes etiquetados.
- No mezclarlos entre ellos si no son compatibles.
- No desecharlos en la alcantarilla.
- Usar la autorización de fuego para los productos inflamables.
La siguiente figura muestra los símbolos que permiten identificar los riesgos en la manipulación de los productos químicos.
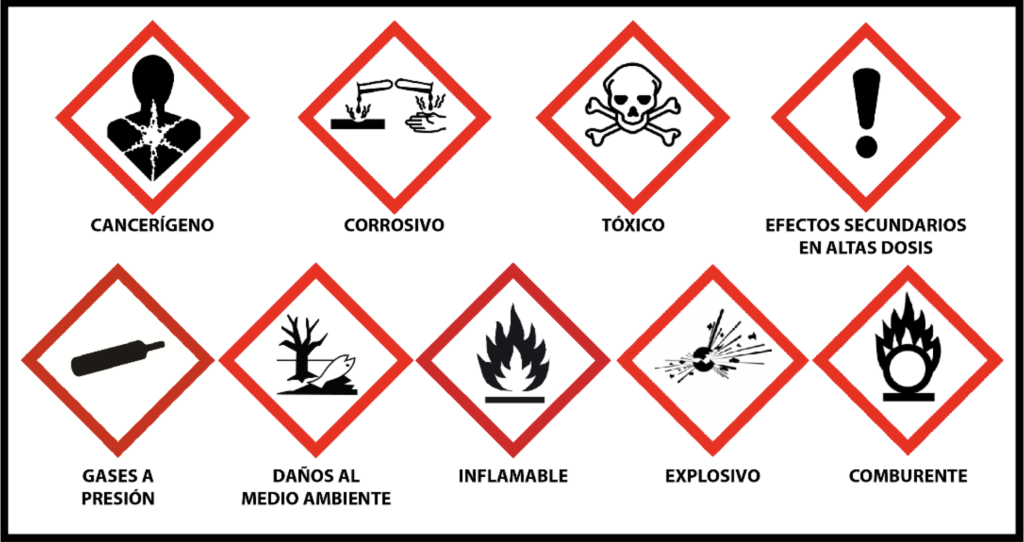
Almacenamiento de productos químicos
Como normas de prevención comunes a cualquier espacio de almacenamiento, se debe tener en cuenta:
- Los almacenamientos nunca deberán obstaculizar la circulación de personas por pasillos o salidas de emergencia.
- Mantener el orden y limpieza en toda la instalación de almacenamiento.
- No almacenar en la misma pila o estantería productos diferentes que presenten posibles reacciones peligrosas.
- Realizar inspecciones continuas por el responsable del almacenamiento.
Específicamente, en el almacenamiento de productos químicos, las medidas de buenas prácticas son, principalmente:
- Las áreas de almacenaje provisional de sustancias peligrosas deben estar protegidas, en la medida de lo posible separadas de otros procesos, en salas independientes o exteriores y debidamente señalizadas.
- Todos los productos deben tener las etiquetas y fichas de datos de seguridad y respectar incompatibilidades y reacciones entre productos.
- Los recipientes vacíos que hayan contenido sustancias peligrosas deben almacenarse en un lugar seguro o ser neutralizadas antes de enviarlos a un gestor de recogida autorizado.
- Los envases empleados deben de ser homologados y en caso de ser de plástico se revisarán con frecuencia y se mantendrán protegidos del sol y del frío.
- Almacenar en lugares refrigerados los productos inestables a temperatura ambiente.
- Mantener una buena ventilación de los locales.
- Reducir al mínimo el uso de equipos que puedan generar chispas.